I've completed another repair trip to replace the transom on my 1964 Dorsett Catalina. I got a couple of major things done, but once again I didn't get as much done as I had hoped for. I had a couple of set backs, and I made a few beginner mistakes. I lost a couple of days due to the weather, etc., but I'm still enthusiastic and determined. At the time of this posting I have been home for about a month. I am starting to realized the amount of work and cost involved in this restoration project. As far as not getting as much accomplished as I wanted to....................it doesn't deter me, it doesn't disappoint me, it just means it's going to take a little longer than I expected. I kind of enjoy the challenge. I am looking forward to my next trip, and planning it as soon as possible. On this trip I wanted to at least get the first piece of transom plywood installed, but a list of things had to be done first. I keep the boat in storage near Ute Lake State Park, at Logan NM (near Tucumcari). It's about 300 miles from where I live in Northern NM. I've scheduled 10 days for this trip, that includes one day to travel there; and one day to travel home. So........., that leaves 8 days. I lose another day of work unpacking, getting the boat out of the storage unit, unloading all the tools, setting up my work area and housing. Then I lose another day putting everything back up, packing tools and cleaning the house before I leave. So.........., that leaves about 5 days or so to work on the boat. I say, "go for it"!
I had some choices to make once I got everything ready to go to work. I need to decide on how I was going to get access to the transom. I had 3 choices:
1. Uncap the top and remove it.
2. Cut the topcap on each side, just in front of the splashwell. Then remove the splashwell.
3. Uncap the top about 5/8 of the way on each side from the rear of the boat forward. Then jack up the splashwell high enough to gain access to the transom.
I decided to try choice #3 first. That way if I needed to camp at the State Park, I could still stay in the cabin of the boat (I'm staying at a friend's cabin, but he closes and winterizes it during the winter).
So, that's where I started...........
I had already uncapped it about 1/2 way on my last trip to remove the old plywood. So now I decided to uncap it about another two feet on each side. That means I needed to remove the stainless steel wire staples that hold the topcap to the hull. But before I could do that I needed to drill small pilot holes next to the staples, to use to re-align the topcap when it was time to replace it. Drilling the holes and removing the staples took quite awhile. The wire staples are a lot tougher than you might imagine. I had to use a hammer and a small chisel to unbend the bottom part of the staple, before I could pull them through to remove them. I also had to un-bolt the rubrail a little farther on each side. This is where I hit one of the set backs I mentioned in the first paragraph. I got the port side un-bolted, although I had to wrestle with a couple of rusted bolts. On the starboard side I only had two bolts to go when I came to one that wouldn't let go. On the outside portion of the rubrail under the rubber insert, it had a flathead standard screw. On the inside portion of the rubrail, right up against the cabin bulkhead; was a 3/8'' nut. I tried every trick in the book. I placed a box end wrench on it and taped it to the wall against the bulkhead, climbed out of the boat and tried to unscrew it with a large screwdriver. Either the wrench would slip off or flip off when I applied pressure, or the screwdriver would pop out of the slotted screw head (I was about to ruin the screwhead). Over and over, in and out of the boat, again and again. Then, I used vice grips instead of the wrench, same story. Then I thought OK......... I'll heat it up. I made a heat shield out of aluminum foil and an aluminum pie plate. I used a small adjustable propane torch. But the bolt was just to close to the wall, and I was afraid I would damage it. So I stopped. Then, I drove into Logan,NM, to the auto parts store (it's also a hardware, plumbing and feed store) and ordered an impact screwdriver. The kind you hit with a hammer to loosen the screw, and with the impact it wouldn't slip out of the slot. They said they could have it there by eight o'clock in the morning. OK.....I'll pick it up in the morning.
I picked up the impact driver the next morning and went straight to work on the stuck bolt. I made sure the impact driver was turning in the right direction to loosen, put it on the screw and gave it a whack. Nothing moved...........gave it another whack, and another, nothing moved??? I tried it on a screw on my pickup, it loosened it. Tried it again on the boat, nothing. I finally decided that there was to much "give" in the fiberglass of the boat for the "impact action" to work as it should. What next.....??? I'll try to drill the screw out. The screw was stainless steel, therefore very hard. I broke two 1/8" drill bits in a row. I am doing everything I can not to damage the boat any further. I had this boat looking really good before I damaged the transom. I finally gave in and did something I didn't want to do.............I drilled through the rubrail on both sides of the screw, and "grabbed" it with a pair of needle nosed vise-grips. Then I went inside and finally loosened the nut, and removed the screw. I brought the screw and nut home with me and I keep it on my desk, to remind me sometimes you have to persevere.
I had wasted a lot of time removing the screw and nut. The weather was supposed to start turning bad tomorrow. I had to keep working if I wanted to accomplish everything I had on my to-do list. Now that I had a portion of the boat topcap loosened, I could attempt to jack up the splashwell for access to the transom. I gathered the materials, and built an elevated pad for the floor jack to rest on. I used a 2''x4'' under the splashwell for the jack to lift against. Once everything was in place, I started jacking the splashwell up. Everything went pretty well, I proceeded s-l-o-w-l-y. I got out of the boat and checked for excess stress areas, every 2 or 3 inches of upward lift. Everything looked good, after lifting the splashwell about 10"; I got out and checked for stress areas again. I could still actually lift the splashwell by hand, no problem. I only needed to lift it about 14" or so, four more inches to go. I jacked the last 4 inches very slowly. When it was high enough, I let out a deep breath and smiled. I didn't move for a while, I just let everything rest in place, and become accustomed to its new spot. This is when I hit the second set back I mentioned in the first paragraph. I was placing supports under both sides to hold it in place, so I could remove the jack. CRACK!!! ........Huh??? What??? I got out and looked around and discovered a crack in the fiberglass on the starboard gunwale, where it turns upward to form the cabin.
gun·wale
/gənl/
noun
noun: gunwale; plural noun: gunwales; noun: gunnel; plural noun: gunnels
- the upper edge of the side of a boat or ship.
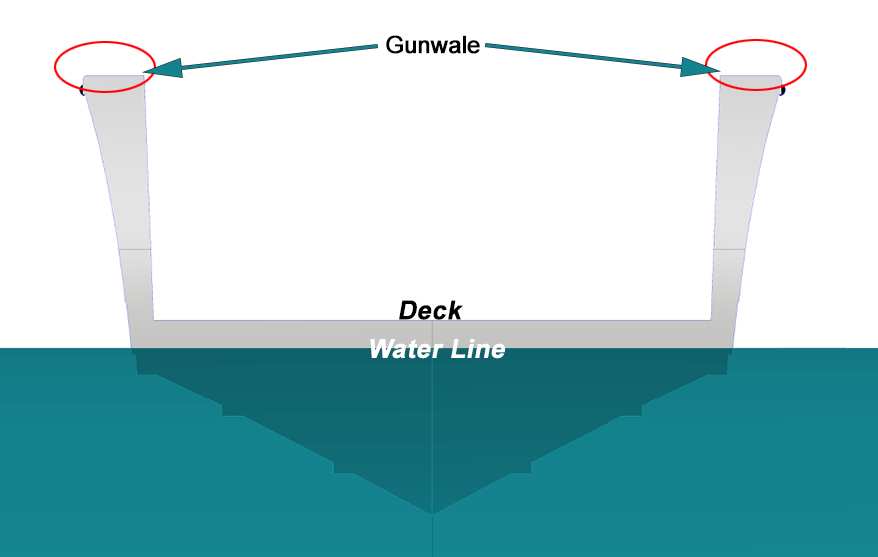
I went back in the boat and removed the supports, and lowered the jack to relieve the stress on the gunwale. I started looking for the reason the gunwale cracked instead of lifting like it should have. It didn't take long to figure it out. I had forgot to remove the screws that go through the roof crosspiece behind the cabin bulkhead, that hold the topcap in place. A mistake only a beginner would make, i just hadn't thought of it. (aahhhhhhh!!!)
Well,..........what now, what to do next??? I sat down and thought about it for awhile. I could repair the crack, no big deal. I decided to make a temporary brace 5' long, out of a 1''x4''. Then, place the brace on the outside of the gunwale, with the crack in the middle area of the brace. Then, jack up the topcap again and go on from there. But first, I needed to re-attach the topcap to the hull so that it would be straight when I attached the brace. Thankfully, I had drilled 1/8'' pilot holes in the topcap and hull. I used 1/8''x3/8'' thread rolling screws (used to fasten plastics) to join the topcap and the hull. When the time comes, I will use these same screws and 3M 5200 adhesive; to permanently bond the topcap and hull. I got the topcap and hull put together just before dark. The weather was supposed to turn bad tomorrow, it was already getting cloudy and windy. I called it a day.
The next morning was windy, cloudy and cold, the predicted high temperature for the day was 34 degrees. I already had a plan in mind of what I was going to do today. I had purchased a new Craftsman (job site) Table Saw. I bought it online, specifically for this project. I had it shipped to the Post Office in Logan, NM, via General delivery. It came in a large box and it saved me having to haul it all the way there. So, the plan for today was to go to the Post Office and pick it up, bring it home and assemble it. And, one final chore, I usually always bring my dog "Sugar" with me for company, she's always ready for an adventure. She loves to go on the boat, and I consider her part of my crew with the rank of "swabbie". Anyway, she was getting restless so I needed to take her for a run today too. Late in the day it started to rain. So, that's how I spent this cold, wet day.
It drizzled rain most of the night, but by ten o'clock the next morning it was mostly sunny. The high for today was supposed to be in the upper 40's. The wind had stopped blowing as hard, but it was still breezy. I went to work and placed the brace on the gunwale. I took out all the thread rolling screws and jacked up the topcap, this time without incident. As it was already about 1:30 in the afternoon, I wanted to start work on the transom pattern right away. Instead, I noticed that material from the old fillets and fiberglass residue was still attached in the corners and along the edges where the old plywood used to be attached. It would have to be removed before I could go any further. I was anxious to start cleaning the old fillet material. I had very little experience in fiberglass grinding and sanding at this point, and I wanted to see what it was like. I started with the oscillating multi-tool (OMT) with a serrated cutting blade and made some progress. I couldn't believe the amount of dust it produced. I had to clean both sides of the transom, the bottom was already clean. After a while I switched from the serrated blade to a rasp attachment on the OMT. It produced twice the amount of dust. For awhile, I was working outside in a breeze, and the amount of dust was very noticeable. Then, the rest of the work was sanding inside the boat, with a lot of airborne dust. I decided to be smart, and use my respirator. I had used the respirator on my last trip but only for a very short time. This was going to be its first real test. It took about three hours to clean the edges and a few other spots. How did the respirator do??? It was not as comfortable as I had hoped for. I wear glasses (I'm old) and the respirator is a full facemask type, it pressed my glasses against the bridge of my nose. It became uncomfortable very quickly. The respirator has filtered, constant flow, fresh air from a small rechargeable air-pump that you wear on your belt. The air flow was pretty weak until I removed the rubber diaphragm in the one way, fresh air feed valve. With forced air I don't believe you need the one way valve, after removing the diaphragm the air supply was adequate. Helmar had sent me the link to buy one, but I was cheap and bought a similar cheap knock off brand on Ebay. I should have spent the money and bought the one Helmar recommended. After doing about 3 hrs of sanding fiberglass, I can understand why people dread it. I was fairly covered with white fiberglass dust, my hair, my arms, my clothing, pretty much all over. Even with the respirator being uncomfortable, I'm glad I used it. It was late afternoon by the time I finished sanding and cleaning the edges. Working alone, and doing all the things that I had accomplished for today, wore me out........ I called it a day.
The next day I didn't start work until it had warmed up a little, about 10 o'clock. With the old fairing and fiberglass material removed, I could start building the transom pattern. Using the newly assembled Craftsman table saw, I ripped some 2'' strips out of the door skin to use as material to build the transom pattern with. I took the 2'' strips of door skin that I had ripped, measured and cut them to form the pieces of the pattern. Then, I hot glued all the pieces together forming a skeleton type frame around the outside edges of the transom. Then, I started to hot glue Popsicle sticks to the frame as Helmer had explained to get precise measurements. This process went very quickly and easily. In just a little while I had the transom pattern finished. On a earlier repair trip I had bought two sheets of 3/4" Marine Plywood, I had them stored in my boat storage unit (indoor). My boat storage unit was about 3 miles away, so I needed to go there and cut two oversized transom blanks from the 3/4'' plywood.
I knew I was starting to run short on time, so I needed to keep working and try to hurry. I was starting to realize that I may not get the transom plywood "glassed-in" on this trip. Well, it is what it is.........."Que Sara, Sara" (what will be, will be). I grabbed "Sugar", a couple of saws, and an extension cord, threw 'em in my truck and headed to my boat storage unit. I thought it would be easier to cut some transom blanks out of the 4'x8' plywood sheets there, rather than wrestle the heavy 4'x8' sheets back to the cabin. There's no electricity in the boat storage unit. However, I have a 3000/6000 watt inverter and a 4 battery setup, wired in my truck. More than enough power to run the saws. I used the tailgate of my truck and two sawhorses to cut the plywood on. After cutting them, I loaded the two transom blanks in my truck and went back to the cabin. It was late afternoon, but I thought that I would have enough time to transfer the pattern onto the plywood and cut it. I set up two sawhorses and put the plywood blanks on them. I placed the transom pattern on the plywood blank, then I clamped the transom pattern to the plywood blank. I wanted to make sure nothing would move and that I would get an accurate "cut". I made a mark at the farthest point on each Popsicle stick, all the way around. Then I used a 18'' straight edge to connect all the marks together. When I was finished I had a "mirror image" of the transom drawn on the plywood blank. I decided to keep working after dark to complete the cutting of the plywood blank. The place I was staying had a porch light, and I used it to keep working. I used a jigsaw with a new blade, and I took my time to make sure I didn't make any mistakes. All in all, it took a little over an hour to cut the new transom. I was happy with the way it turned out. I was also tired and I called it a day. I could only work on the boat until noon tomorrow. Then I had to take the boat back to the storage unit, and start packing for the trip home. The weather was predicted to change tomorrow, to freezing rain and snow (great!) for the next two or three days.
The next morning was overcast and windy. I waited until about ten o'clock for it to warm up enough to start work. I cleaned all the tools and materials out of the boat. I left the topcap in the supported, jacked up position and used ratchet straps to secure it in that position. I backed my pickup into position and hitched the boat to it. I had to load everything that was going to stay with the boat in the storage unit (tons of tools, materials, including the new table saw). After everything was loaded, I towed the boat and equipment to the storage unit. Once I was at the storage unit, I have to make myself go into "low gear" and take my time backing the boat into the storage unit. It's not that hard to do, but I'm still very careful and take my time. Once that was done, head back to the cabin and start packing. The next day is reserved for cleaning the cabin and loading and servicing my truck for the trip home (about 300 miles).
The morning I left for home, it was spitting snow. I stopped in Tucumcari, NM on the way home to look at another Dorsett Catalina. The man that owns it has asked me a couple of times to come by and look at it, he wants to sell it. You can see it in my post in the Classic Boat Sighting section, title "19?? Dorsett Catalina". It looked a little "rough", but I'd like to buy the windshield from him......?? The rest of the trip home was uneventful, just long.
Some observations and thoughts
I am learning that work takes time, especially working alone. I used to think "I'll go out and jump on it, and I'll be done in no time". Well,..............it doesn't always work like that. I'm finding that "prep work" takes a lot of time before you can do the actual work. I need to figure that in before I set my expectations.
I am thinking about uncapping the top half of the boat, and bringing home just the hull and continue the work here (transom, stringers, floor). I would get the work finished a lot sooner, at a lot less cost. Once the work is completed, I want to take the boat to Lake Powell in Arizona for a vacation. Hopefully in early October. I've already started getting ready for it, I just installed airbag suspension in my pickup to help carry the load of the boat and trailer.
After reading Helmar's posts on his "16' Bell Boy Restoration". I think I need to turn my topcap upside down and replace the wood in the gunwale's, also. This is something I never would have thought of, thank you Helmar for your posts.
I am looking into permanent under floor gas tanks or building seating that will conceal them. I am wanting at least 30 gal. storage, probably in two tanks. I need to get to the point where I can cut the floor out and see whats under it, see how much room there actually is.
I am actively searching for a 85 - 90 hp Outboard motor, good running, with no issues. Ideally with controls, tilt trim, all cables. I'm also tossing around the idea of twin motors, 2 - 50 hp white Mercury's. I'm still researching the controls needed for twins. I'm thinking about the pros & cons of twin motors.
Well, that's about it for this update. Check out the pictures I'm including................
Comment